The Curious Case of Corrosion, Part 2
Corrosion, Part 2
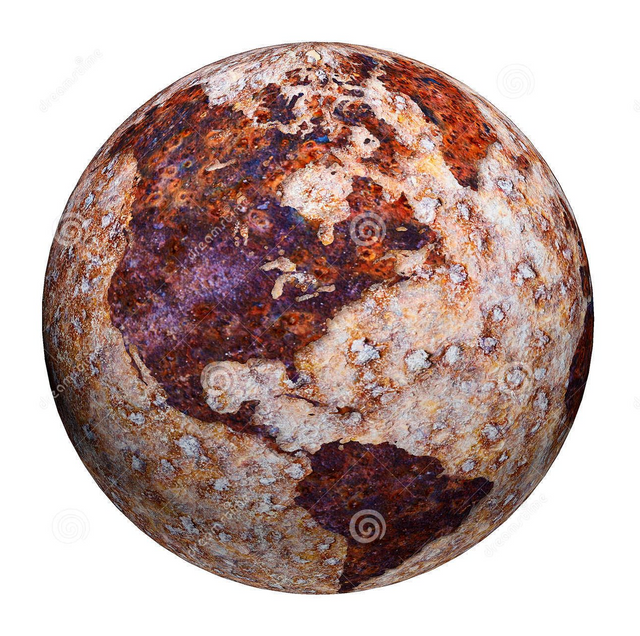
Corrosion
As promised on my previous post, this is a continuation on Corrosion but in this post, we will be exploring the different branches of Corrosion, some new; some old, and trying to understand the type of corrosion as well as the initiating factors in the surrounding environments, the corrosive mechanisms that occur, explanation through applications in industry for a few examples as well as the most common and useful methods of prevention.
As we may have gathered from my previous post, the main branch of corrosion that we will be exploring is Wet and Dry Corrosion. For those who may not have read my last post, wet corrosion (also known as Aqueous Corrosion) is a form of corrosion that occurs around room temperature as well as when water is present. Dry Corrosion occurs when no water is present and generally at extremely elevated temperatures. Between these 2 sub branches of corrosion, the aspect that we will be focusing on is Wet Corrosion. Wet Corrosion can be split up into the following branches:
- Uniform Corrosion
- Galvanic Corrosion
- Crevice Corrosion
- Pitting Corrosion
- Intergranular Corrosion
- Selective Leaching
- Erosion Corrosion
- Stress- Corrosion Cracking
Uniform Corrosion:
This type of Corrosion occurs due to chemical as well as electrochemical reactions that spread at a constant rate, or uniformly (hence the name) over the entire surface of the exposed metal. Consequences of Uniform Corrosion includes the thinning of the metals surface, leading to failing of the materials strength and thus breaking or collapsing of material.
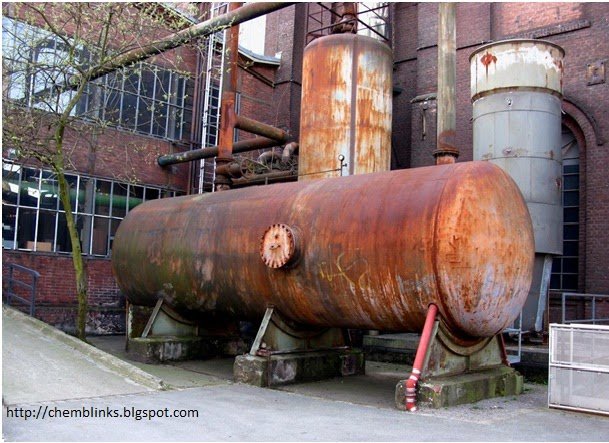
Uniform Corrosion Upon a Tank
If a metal is submerged in a bath of acid (such as steel in a sulphuric acid bath), the acid will corrode the metal uniformly at a constant rate over the entire exposed surface area. This branch of Wet Corrosion is considered to have the largest consumption of metal than any other branch of corrosion, but, there are certain steps that can be put into place to prevent this type of corrosion from occurring. Such methods are the use of proper materials that are needed for that specific application, coating materials to prevent, or add to, its corrosive resistance, the use of inhibitors and even employing methods of cathodic protection.
Galvanic Corrosion:
This branch of corrosion occurs when 2 unlike metals are submerged in an electrolyte solution. This form of corrosion is considered a sacrificial type of corrosion due to the fact that when contact is made between the metals, one metal becomes an anode and the other becomes a cathode. The selected anode metal will now become the less corrosive resistant metal and will subsequently corrode faster than had it being a single metal, while the opposite will happen for the cathode. In doing so, the cathode will survive corrosion while the anode will be sacrificed. For galvanic corrosion to occur however certain requirements need to be accomplished, such as:
- The use of 2 dissimilar metals
- Physical contact between these 2 metals
- Metals must be submerged in the same electrolyte
The following factors have been known to affect the rate at which Galvanic Corrosion occurs:
- Environmental Factors- depending of the type of environment, the corrosion rate can be affected by the natural aggressive corrosive environment. Since it is known, from Part 1, that every area in the world is corrosive to a certain degree, we should therefore understand that the moisture in the air will act as the electrolyte in these circumstances. The degree of corrosion is directly proportional to the amount of moisture present in the air as well as the type of moisture as certain vapours are more conductive than others.
Visual Decription of the relationships
The Distance Effect- if the electrochemical cell is connected in a laboratory, a salt bridge, also known as a junction, will be used to facilitate in the consumption of free ions in the electrolyte that are produced through the reaction. The closer the involved metals are to the junction, the greater the degree of corrosion upon the anode. It should therefore be noted that with increasing distance from the junction, the degree of corrosion decreases and thus portrays an inversely proportional relationship.
Area Ratio- The use of the anode is to allow the anode to corrode while protecting the cathode. If a large cathode and a small anode are required to react upon each other, a small degree of corrosion will act upon the anode. Due to this unfavorable area ratio, the cathode will continue to corrode once the anode has corroded completely. For maximum optimism of this corrosion (that is, prevention of cathodic corrosion), an anode larger than that of the cathode should be used.
Preventive methods for Galvanic Corrosion includes avoiding contact of these dissimilar metals by method of insulations or to allow contact of 2 similar metals, avoiding the unfavorable area ratio as mentioned earlier, apply corrosion protective layers to the metals and use inhibitors.
Crevice Corrosion
When small amounts of still liquid is allowed to collect in the crevices of metals and other semi-enclosed areas of metals, it is vulnerable to Crevice Corrosion. Also commonly referred to as Gasket or Deposit Corrosion, it usually occurs under bolts or surface deposits, holes in metal surfaces as well as under gaskets. This branch of corrosion originates in very small openings that may even be microns thick, but if not properly treated, could spread throughout the metals surface.
Preventive methods to Crevice Corrosion include to usually avoid crevices in the design process or to use solid Gaskets instead. If, however, the design does include crevices, the crevice should be filled with a sealant to avoid corrosion from taking place and must be cleaned and inspected regularly, along with the inspection of the equipment, to remove any dirt and deposits that could promote corrosion.
Pitting Corrosion
Pitting Corrosion is a form of Uniform Corrosion and Crevice Corrosion but the only difference is that this form of corrosion only affects certain areas of the exposed steel rather than the entire exposed surface. The product of this corrosive branch is the formation of small holes on the affected surface. These holes may occur in clusters or may even occur far apart from each other (in a dispersed manner). Due to been unidentifiable due to its camouflage of being small and dispersed, Pitting Corrosion may go unidentified for long periods of time, until it results in the severe damage or an overall collapse of the equipment.
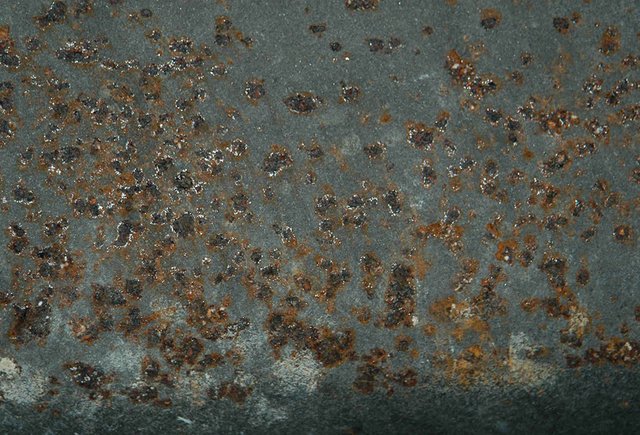
Pitting Corrosion upon a Steel Surface
Factors that affect Pitting Corrosion include:
Chemical Composition in Solution- if the stagnant liquid contains certain element containing ions, the rate of Pitting Corrosion may be increased substantially. When halide ions such as chloride ions, hypochlorites ions and even bromide ions are found in these crevices, Pitting Corrosion occurs violently.
Velocity- since Pitting Corrosion is associated with stagnant conditions, increasing the velocity of the liquid, even minimally, will decrease Pitting Corrosion.
Metallurgy Properties- dependent the material used, the degree of corrosion will differ. Stainless Steel alloys are known to be most vulnerable to Pitting Corrosion than any other alloy.
Prevention of Pitting Corrosion have the same points as Crevice Corrosion due to this form of corrosion being an intermediate form of corrosion between Crevice Corrosion and Uniform Corrosion (that is overall corrosion).
Intergranular Corrosion (IGC)
Similarly, to Pitting Corrosion, IGC is a localized form of corrosion as in the sense that it attacks certain regions of an exposed material rather than the entire surface. The grain boundary of the material (microscopic region) is attacked while the grain interior is left unharmed. This causes the material to fall apart and disintegrate due to impurities upon the grain boundary that will lead to IGC.
Selective Leaching
The removal of an element from a solid alloy due to corrosion is referred to as Selective Leaching. The most common element that is often removed is Zinc, therefore, a process known as dezincification was identified. Zinc is often the most attacked element by corrosion due to Zinc making up a large part of the chemical composition of most metals and steels.
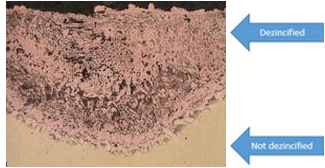
Difference of Materials
There are a few types of Dezincification which show certain properties of the previously mentioned branches of corrosion, which include:
Uniform- zinc is depleted from the entire surface of the material, generally in highly acidic regions.
Plug-type- can be considered localized dezincification as zinc is removed from only certain regions of the exposed surface. Known to occur in environments that are neutral or slightly acidic as well as areas that contain pit-like environments.
Stagnant- zinc removal due to corrosion is favored by stagnant/ non-moving conditions as well as high temperature environments
Methods of prevention against Dezincification include using an alloy that contains a low constitution of zinc in its chemical makeup as well as a change of environment, where it is less acidic and more basic. Additional methods include the use of inhibitors for protection and a non-stagnant environment.
Erosion Corrosion
This is a type of corrosion that occurs due to high speed fluids within a pipe. Movement of high speed fluid wears away the inner layers of the pipe and washes away any layers used for protection of the fluids and pipes. When the layer is removed, corrosion acts upon the unprotective layer at an extremely fast rate. This type of corrosion is extremely dangerous not only for the equipment but also for the health of people. If we are to consume liquids that contains corrosive material as well as protective layers of the pipe, it may cause serious health problems for the person that ingests it.
To avoid these consequences from occurring, certain prevention methods should be put into place. A few examples of prevention methods include the use of materials that are tough enough to withstand the high velocity fluids as well as materials with better corrosion resistance. Designing pipes to avoid the high velocity flow as well as coating the pipes surface with a stronger resistive coat will assist in the prevention of Erosion Corrosion.
Stress-Corrosion Cracking (SCC)
This branch of corrosion is considered more of a consequence due to corrosion rather than a type of corrosion. The combination of corrosive behavior as well as forces that lead to stress is referred to as SCC. SCC often goes unidentified by the eye due to the fact that SCC does not attack the metals surface visibly, instead it leaves fine cracks along the surface that are almost impossible to be identified by the naked eye. It must be noted that these cracks form due to internal corrosion of the material. When a force is now applied in conjunction with the internal corrosion, serious consequences could occur, dependent on the overall strength of the equipment. SCC is known to commonly occur in the cracking of brass which is used in the production of cartridge cases made of brass.
SCC, like any other corrosion branch, has certain factors that could stimulate the corrosive tendencies of the material. These factors include:
Temperature - high temperatured environments will promote SCC
Composition of solution- if enclosed in a pipe, SCC occurs on the inner pipe as Erosion Corrosion will take place
Composition of Metal
Stresses Experienced- the applied force of the stress will relate to the degree of SCC. The larger the force, the greater the degree of SCC. A large range of forces could be applied upon the material to cause SCC including thermal as well as residual stresses.
There are two different types of cracking that could occur which are transgranular and intergranular cracking. Transgranular cracking occurs across grains while intergranular cracking occurs along the grains boundary.
Prevention methods of SCC include the reduction of the stress force applied, reduction in environmental temperature, avoiding SCC promoting environments, use of inhibitors as well as cathodic protection.
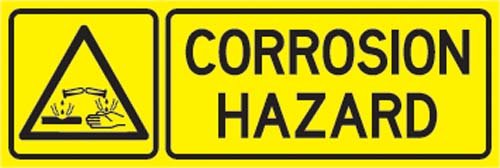
A Corrosive Warning Sign
This is the end on my 2-part series on Corrosion and Corrosion types. I hope that this series has being informative upon all corrosive information.
Images are linked to their sources in their description
The End
References:
[1]https://www.thebalance.com › Investing › Commodities › Metals
[2]https://www.gibsonstainless.com/types-of-corrosion.html
[3]https://www.thomasnet.com/articles/chemicals/corrosion-resistant-coatings
[4]https://www.thomasnet.com/articles/chemicals/corrosion-resistant-coatings
[5]https://s3-ap-southeast-1.amazonaws.com/.../5208_d8e3b23d-25be-4d01-82d4-0cddf...
[6]https://www.emedicalprep.com/study-material/chemistry/.../factors-affect-corrosion/
[7]https://www.nace.org/Corrosion-Central/Corrosion-101/Eight-Forms-of-Corrosion/
Being A SteemStem Member
Corrosion is an enemy of my boat.
Stainless steel corrosion is difficult to spot unit it is to late and failes completely. It is an aerobic metal and needs be uncovered.
I am a big fan of bronze a verry durable alloy.
Very true, corrosion is everyone's enemy. Stainless Steel corrosion is not very publicized because they are supposed to be considered as noncorrosive. Brass is a very good material to be used but the only aspect of problem there would be related to its price range. We need a material with brass's properties and steel's price, haha
Yea price is a problem.
New highend racing saiboats are using carbonfiber chainplates bonded to the hull, carbonfiber masts with dyneema (hdpe) rigging, thereby eliminating any metal being used for their standing rigging.
Amazing times we are experiencing with technological advances.
Nice post btw.
I do not alot of boats but i do about optimization of materials. Carbon fiber is the new trend these days due to its durability and amazingly lightweight properties. Although it may not be as cheap as most materials, for its long lasting use as well as favorable properties, it is definitely worth the price. We should be truely grateful for the advancements in science that we are experiencing.
Thank you very much.
So many artistic installations are making use of corrosion at the moment. I don't really care for it, but it's a unique take on art :)