Equipment of Filtration, Part 2
Filtration Equipment, Part 2
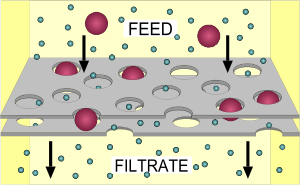
Filtration
As introduced in my previous post, filtration equipment used in everyday industry in chemical engineering is of utmost importance with regard to our everyday living. In this post, I will be introducing a few branches of pressure filters and explaining why a filter press is most oftenly used in industry rather than any other piece of filtering equipment as well as an introduction to filter media.
Filter Press:
As previously mentioned, a filter press is a form of pressure filter which is often regarded as the most used form of filter in industry. A filter press is a piece of equipment that contains parallel sets of plates, with constant widths between each plate.
Each plate is covered with a filter medium through which the slurry, as well as the filtrate from the previous plate, is passed through. This ensures that all liquid that is identifiable, on a macroscopic level, is removed from the slurry. This simple procedure ensures a high purity cake formation which has minimal or no moisture therefore increasing it’s monetary value in industry.
The slurry entering each medium experiences a certain substantial pressure difference, which facilitating in the overall movement of the slurry. Once the slurry has been passed through the medium, the cake remains behind and is trapped by the medium. Before the cake from each plate can be retrieved, the filtrate from each step must be discarded off first. This is done by allowing the filtrate from every plate to be passed through the last plate. At the end of this last plate, a discharge pipe is fitted. This allows the filtrate to be disposed off from the system and thus only leaves behind the cake. Dependent upon the type of filter press, the method to retrieve the cake may vary. In most cases, underneath the series of plates, is a long horizontal plate that spans the entire range of the vertical plates. It is upon this plate that the cake, from each plate above, falls on to and is further refined. The size of the plates used may vary in design but the most oftenly used and optimal plate shape is a square. The dimensions of the plates can range from 150 mm up to 2 m long.
For filtration that is carried out at a constant pressure within the filter press, the following equation is used to calculate the time required for filtration:
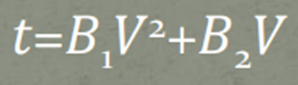
We optimise this equation by including a time of dismantling and assembling the press, which is denoted by the symbol t'. Due to this reason, the total time is regarded as (t + t'). By use of this new time, the filtration rate now derives to:
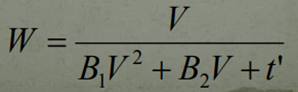
Advantages and disadvantages of the filter press include:
- Being that of a simple design, it can be used for a large range of materials of different properties of cake thickness.
- Having a low maintenance cost.
- The favourable ratio of having a large filtering area on a small floor space available.
- Operation at high pressures are usually possible.
- It is equally suitable for operation whereby the cake or the liquid that is been filtered is the main product.
- A filter press unfortunately suffers from intermittence in operation and requires continual dismantling in industry.
- A filter press is often fairly heavily dependent upon physical labor.
Before introducing the different types of filter presses used in industry, it is important to note that the most basic design of a filter press is that of the aforementioned description in which it consist only of square parallel plates. Through the years of development of this filter press, newer and more improvised versions were developed to add a sense of optimisation as well as individuality to the equipment (as the new equipments had specific duties to fulfill at an extremely high level of accuracy). After these years of development, 2 filter presses in particular were used most in industry. These 2 presses were regarded as:
Pressure Leaf Filter:
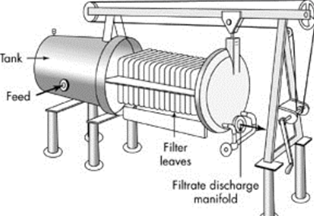
A Horizontal Pressure Leaf Filter
A pressure leaf filter is the lesser used filter of the two main filter presses in industry. The reason why a pressure leaf filter is used is due to this form of filter being able to operate under extremely high pressures in comparison to that of a plate and frame press. Other properties of a pressure leaf filter that are far superior to that off a plate and frame press is due to its ability to economize and cut down the need for physical labour as well as to perform a better washing of the cake produced.
Rotary Drum Filters:
A rotary drum filter is the more widely used filter in comparison to that of pressure leaf filters and is coincidentally the most widely used form of vacuum filter. Due to its specifications, it can be operated as a pressure filter as well as a vacuum filter. This is the reason why the rotary drum filter is one of the most economical and most used filters in the world today.
A rotary drum filter is essentially a drum type vacuum filter that has multiple compartments that consists of a drum rotating along a horizontal axis. For maximum optimisation of filtration, the drum is partially submerged in a trough, whereby material that needs to be filtered is fed through.
Filter Media:
For filtration to occur, we understand that a filter medium is required to allow the filtrate and the solid particles to be separated. For this to occur at optimal efficiency, the correct type of filter media is required, as the choice of filter media chosen will not only affect filtration efficiency, but it will also determine the overall success of the operation. The requirements taken into consideration before choosing the type of medium used:
- The media’s ability to retain solids that are being filtered and to produce a clear filtrate.
- Must not plug or blind the flow of the filtrate through the media.
- Must not be resistant to any process conditions.
- The media must be of sufficient strength to support the pressure difference across the media and in turn support the filtering pressure.
- Must have the ability of easy discharge of cake in a constant and clean process.
- The media must be of minimum cost but must be of acceptable quality.
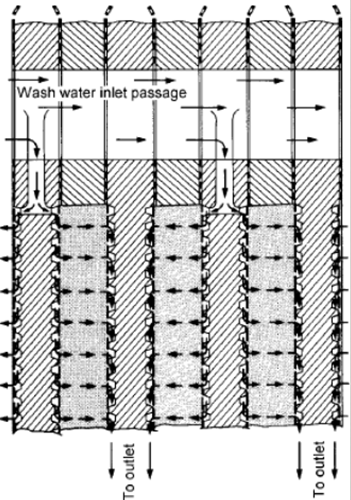
Capturing Cake In a Filter Press
This brings us to the end of part 2 of filtration equipment and has allowed us to introduce the concepts of pressure filters as well as an introduction to filter media. In part 3 of filtration equipment, I will introduce the important sets of information regarding the types of Filter media as well as filter aids.
Images are linked to their sources in their description
The End
References:
[1]https://www.mwwatermark.com/en_US/what-is-a-filter-press/
[2]https://www.3diequipment.com/different-types-of-filter-press/
[3]https://www.mwwatermark.com/en_US/filter-plates/
[4]Unit Operations of Chemical Engineering by McCabe W.L., Smit J.C. and Harriot P (McGrawHill, 7th Edition, 2005)
[5]Coulson and Richardson's Chemical Engineering. Vol. 2, Oxford, ButterworthHeinemann by RICHARDSON, J. F., HARKER, J. H., BACKHURST, J. R., & COULSON, J. M. (2002).
Being A SteemStem Member
Would be nice if you gave us a few examples of where these filters are used exactly. When I started reading, for instance, I was imagining public water filters or some such.
I will start doing so on my post to follow, thank you for bringing it to my attention Alexander. Broadening horizons is very important.
If you’re looking to upgrade your home with attractive, low-maintenance gutters, look no further. The experts at LeafFilter Gutter Protection are ready to provide you with the best service, by offering gutter replacement, cleaning, and repairs in addition to installing gutter guards. From its innovative LeafFilter North reviews design and award-winning technology to its professional installation, LeafFilter protects the value of your home and is the perfect complement to your roof with installation available on new or existing gutters. Contact LeafFilter to schedule a free estimate today! Senior & military discounts available.